Grau ist alle Theorie! Daher gibt es für Studierende an der Fachhochschule zahlreiche Möglichkeiten, sich produktiv auszutoben. In vielen Fachbereichen unterstützen Lehrende und Laboringenieurinnen und -ingenieure kreative Köpfe dabei, Gelerntes umzusetzen, Ideen in Greifbares und Träume in Wirklichkeit zu verwandeln.
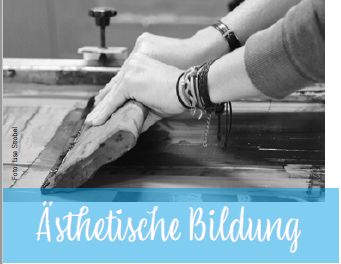
Vielfältige Möglichkeiten sich kreativ auszutoben, bietet der Fachbereich Soziale Arbeit und Gesundheit – insbesondere im Bereich Ästhetische Bildung. Im November 2015 eröffnete Prof. Dr. Sabine Grosser , Leiterin des Bereichs Ästhetische Bildung, im 8. Stock des Gebäudes C3 das Ästhetik- und Lernlabor. In die Entwicklung des Raums waren neben den Lehrenden auch Studierende einbezogen. In der Kreativphase entwarfen Studierende Lernräume. Sie entwickelten Modelle und schließlich nutzbare Multifunktionsmöbel und Leitsysteme für Gebäude, die sich im praktischen Einsatz an der Fachhochschule und darüber hinaus – zum Beispiel in einem Leitsystem für eine Flüchtlingsunterkunft – bewährt haben.
Zur Fertigung stehen Werkzeuge für Holzbearbeitung und Siebdruck zur Verfügung. Nach einem Einführungsseminar können Studierende an der Siebdruckmaschine originelle Motive und Botschaften in maschinengestützter Handarbeit auf T-Shirts und Leinwände drucken. Trotz guter Ausstattung sieht Sabine Grosser noch Luft nach oben: „Wünschenswert wäre eine Werkstattbetreuung, um den Zugang für die Studierenden flexibler gestalten zu können.“
An den Laptops, Video- und Datenprojektoren sowie der Audiotechnik des zu diesem Bereich gehörigen Medienlabors können eingewiesene Studierende auch zu außergewöhnlichen Zeiten arbeiten. Im Rahmen von Studienprojekten können sie auch Spiegelreflexkameras, Aufnahmegeräte und Laptops für einen ganzen Tag entleihen, wenn sie beispielsweise mittels Videoaufzeichnungen Gesprächsführung erforschen möchten.
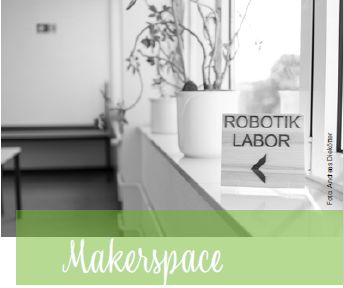
Ob eine Idee dazu taugt, Probleme zu lösen, Menschen zu beflügeln oder sogar die Welt zu verändern, erfährt erst, wer sie in die Tat umsetzt. Gegenwärtig arbeiten Prof. Dr. Robert Manzke und Prof. Dr. Jens Lüssem vom Fachbereich Informatik und Elektrotechnik gemeinsam mit Prof. Dr. Heidi Kjär vom Fachbereich Medien an der Einrichtung eines sogenannten Makerspace , einer Reihe von Arbeitsräumen, die mit digitalen Werkzeugen ausgestattet sind.
In der großen Werkstatt im ersten Stock des Gebäudes C12 sieht es nach Arbeit aus. Neben vielen Laptops stehen Oszilloskope und Lötstationen; auf den Tischen liegen Akkuschrauber, aus Schubladen hängen Kabel. In der Mitte des Raumes steht ein großer Tisch, der allerdings mehr ist als ein Möbelstück. Durch Infrarot-Reflektion erkennt das Gerät, dessen Oberfläche ein riesiger Bildschirm ist, die Position von Fingern. „Gut, um innovative Spiele zu entwickeln, aber man kann auch Sinnvolles dafür programmieren“, erklärt Hannes Eilers, der hier als Laboringenieur tätig ist. Beispielsweise einen Minifußballplatz, auf dem kleine, selbstgedruckte Roboter mit eigener künstlicher Intelligenz autonom gegeneinander Fußball spielen.
In einer Ecke des Raumes stehen zwei Replikatoren. Der MakerBot ist ein 3D-Drucker, mit dem Studierende Werkstücke und Prototypen herstellen. Aus einer feinen beweglichen Düse rinnt heißer Kunststoff, aus dem sich über mehrere Stunden in einem steten Hin und Her das Chassis eines Quadrocopters formt. Daneben steht der Formlabs Form 2, ein Stereolithographie-Drucker. Ein Laser fährt bei jedem Schritt über den Ausgangsstoff, um die gewünschte Form zu schaffen. Dabei wird das Werkstück nach und nach aus einem Flüssigbad aus Photopolymer herausgezogen. Die Präzision der Geräte ist so beeindruckend, wie die Vielfalt ihrer Anwendungsmöglichkeiten. Wenn die entsprechenden CAD-Daten vorlägen, wäre es sogar möglich, provisorische Zahnkronen aus Kunststoff zu drucken. „Wir wollen, dass die Studierenden hier kreativ werden. Aber wir achten auch darauf, dass die Projektideen einen technischen Anspruch haben. Schließlich sollen die Arbeiten ja auch in Credit Points münden“, fasst Prof. Manzke die Rahmenbedingungen zusammen.
Ein angrenzender Raum wird gerade eingerichtet. Bald stehen hier vier hüfthohe Tische, bereits jetzt hängen von der Decke würfelförmige Steckdosen. Teams mit bis zu fünf Studierenden sollen hier gemeinsam an ihren Laptops Produktideen entwickeln und in Prototypen umsetzen können. Mobile Stellwände erlauben eine individuelle Raumaufteilung. An einem Whiteboard oder mit einem Beamer können Teams ihre Pläne, die Robotik und kreative Technologie zusammenbringen, großflächig an die Wand werfen.
Das Schmuckstück der Hightech-Werkstatt ist ein Lasercutter. Digitale Vektorgrafiken geben vor, wie der Laser punktgenau durch Holz und Edelstahl schneidet. So lassen sich in kurzer Zeit Bauteile fertigen und Rohlinge basteln, anhand derer sich schließlich zeigt, ob sich Ideen verwirklichen lassen. „Dieses Rapid Protyping ist auch für Studierende interessant, die sich mit einer Geschäftsidee selbständig machen möchten. Sie können in kurzer Zeit Prototypen erstellen und potenziellen Investoren das geplante Produkt in die Hand geben“, erklärt Manzke. Aus dem Zusammenspiel von Kreativität und High-Tech-Maschinenpark ist bereits viel Beeindruckendes entstanden; Makerspace-Hiwi Reimar Zech z.B. baute mit seinem Projektteam ein Skateboard mit Teilen aus dem Lasercutter und 3D-Drucker, das durch einen Elektromotor angetrieben und durch ein Smartphone gesteuert wird.
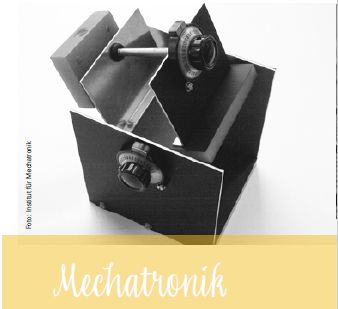
Carsten Glüsing und Matthias Teichmann sind die Ansprechpartner der Werkstatt am Institut für Mechatronik. Gemeinsam mit Hiwis und Mechanikern betreuen sie CNC-Fräsen und Ätzmaschinen, die dazu dienen, mechanische Bauteile zu fertigen und Leiterplatten aus Epoxyd-Material herzustellen. Bevor bastelwütige Studierende ihre Ideen hier verwirklichen können, müssen sie vorsprechen, sich und ihr Anliegen vorstellen und sich mit den Sicherheitsbestimmungen vertraut machen. Meist haben Interessierte einen Großteil der Arbeit bereits erledigt, bevor sie zu ihm kommen, weiß Glüsing: „Grundlage für die maschinelle Fertigung in unserer Werkstatt sind technische Zeichnungen, die am Computer erstellt werden. Auf der Basis dieser Daten können die Maschinen dann loslegen.“
Studierende, die eine Einweisung erhalten haben und die Geräte sicher bedienen können, dürfen in Leerlaufzeiten auch private Probleme beheben. „Häufig kommen Studierende, an deren Mobilgeräten Ladestecker, Buchsen oder Gehäuseteile defekt sind. Wenn sie die Materialkosten bezahlen, können sie für sich hier Ersatzteile herstellen“, erklärt Glüsing.
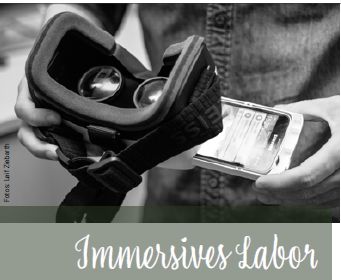
Das „Labor für Immersionsforschung und interaktive Medien“ – vom betreuenden Team LINK genannt – ist ein Forschungs- und Entwicklungsraum für Studierende, die sich dafür interessieren, wie man Inhalte für neue Medientechnologien analysieren und produzieren kann. An den Arbeitsplätzen, die an das Labor angegliedert sind, haben die Studierenden die Möglichkeit, vielfältige Medienrealitäten zu erschaffen. So programmieren sie beispielsweise mit Unity3D virtuelle Welten, um diese später erkunden zu können – und sich dabei zu fühlen, als wären sie mitten drin. „Für ein realistischeres Erleben von Virtuell Reality Umgebungen besitzen wir eine Auswahl an VR-Brillen“, erklärt Prof. Dr. Patrick Rupert-Kruse , Leiter des Instituts für immersive Medien, zu dem das Labor gehört. Die helmartigen Geräte enthalten knapp smartphone-große Bildschirme und Linsensets, wodurch das computergenerierte Bild fast das gesamte Sichtfeld der Nutzerinnen und Nutzer ausfüllt. „Der Blick in die Welt wird durch die Bewegung des Kopfes gesteuert – ganz wie in der Realität. So entsteht die Illusion, dass man sich tatsächlich in der am Rechner geschaffenen Welt umsieht“, erklärt Thomas Heuer, Leiter des Labors. Gesteigert wird das Gefühl des Eintauchens in virtuelle Realitäten, wenn man beispielsweise den Arm mit einem Eingabegerät hebt und durch das Headset sieht, wie man in der künstlichen Welt synchron ein Schwert oder Zepter in den Himmel reckt.
Um in solchen virtuellen Umgebungen Bewegungen realistisch abzubilden, nutzt das Labor unterschiedliche Technologien wie beispielsweise die Kinect, die Bewegungen einer Person auf ein digitales Figurenmodell im Rechner übertragen kann. Neben VR-Umgebungen entstehen im Labor aber auch Augmented-Reality-Anwendungen, 360°-Videos und -Audio, Spiele sowie stereoskopische 3D-Bilder und -Filme. „Bei der Konzeption und Umsetzung der Anwendungen, Spiele, Szenarien und Welten geht es uns nicht darum, ein perfektes Produkt zu schaffen, sondern darum herauszufinden, welche Ideen aus welchen Gründen das meiste Potenzial haben“, erläutert Rupert-Kruse.
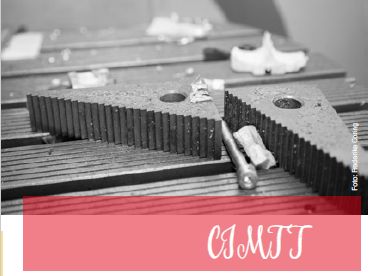
Das Büro von Prof. Dr. Henning Strauß im CIMTT grenzt an eine Werkstatthalle mit einem beeindruckenden Maschinenpark. In einer Vitrine sind zahlreiche Werkstücke ausgestellt, die im Rahmen von Projekten entstanden sind. Die Spanne reicht von detailgetreuen Nachbildungen menschlicher Schädel aus Kunststoff bis hin zu filigranen daumengroßen Schachfiguren mit detailliert modelliertem Innenleben aus der Laser-Sinter-Anlage. „Genauso wie das 3D-Drucken ein additives Fertigungsverfahren, allerdings werden solche Objekte aus einem Pulver hergestellt, das von einem Laser aufgeschmolzen wird und anschließend aushärtet. Viel stabiler und belastbarer als die aus dem 3D-Drucker – aber leider nur einfarbig“, erklärt Strauß schmunzelnd das Verfahren, das hier für die Produktion individueller Bauteile zum Einsatz kommt.
Hinter zwei meterhohen Werkzeugmaschinen, einem 6-Achsen-Bearbeitungszentrum, einer Fräse und einer CNC-Drehmaschine, mit denen Studierende unter anderem Antriebskomponenten herstellen, stehen zwei blank geputzte Schuhe auf Sockeln. Der Glanz der Schuhe ist das Werk eines Roboters, dem Studierende das Schuhputzen beigebracht haben. Die Griffstücke der Bürsten, an denen der Roboterarm mit sieben Gelenken die Bürsten festhält, stammen aus dem 3D-Drucker. Gemäß seiner Programmierung erfasst der Roboter zunächst die Form der Schuhe und holt sich anschließend selbsttätig die geeignete Bürste aus einer Halterung, um an den richtigen Stellen ans Werk zu gehen.
Was dabei heraus kommen kann, wenn ein engagiertes Team von Studierenden aus verschiedenen Fachbereichen auf den Werkzeugpark des CIMTT trifft, kann man am Ende der Halle bestaunen, wo zwei Rennwagen stehen. „Ein Jahr, ein Team, ein Wagen“, bringt es Strauß, der die beteiligten Studierenden als Faculty Advisor Raceyard betreut, auf den Punkt. Auf vielen Teilen des Wagens prangt das markante Raceyard-Logo, sämtlich Teile, die im CIMTT produziert wurden. Vom Chassis über die Sitzschale aus Kohlenstofffaser-verstärktem Kunststoff und die mit Leder überzogene Nackenstütze entspringen alle Bauteile grundsätzlich den kreativen Köpfen der Studierenden; ebenso wie die Programmierung des Elektro-Boliden. Einige Komponenten, deren Eigenfertigung wirtschaftlich nicht sinnvoll wäre, stammen von Sponsoren, „aber theoretisch könnten wir hier das ganze Auto herstellen“, beschließt Strauß den Rundgang.