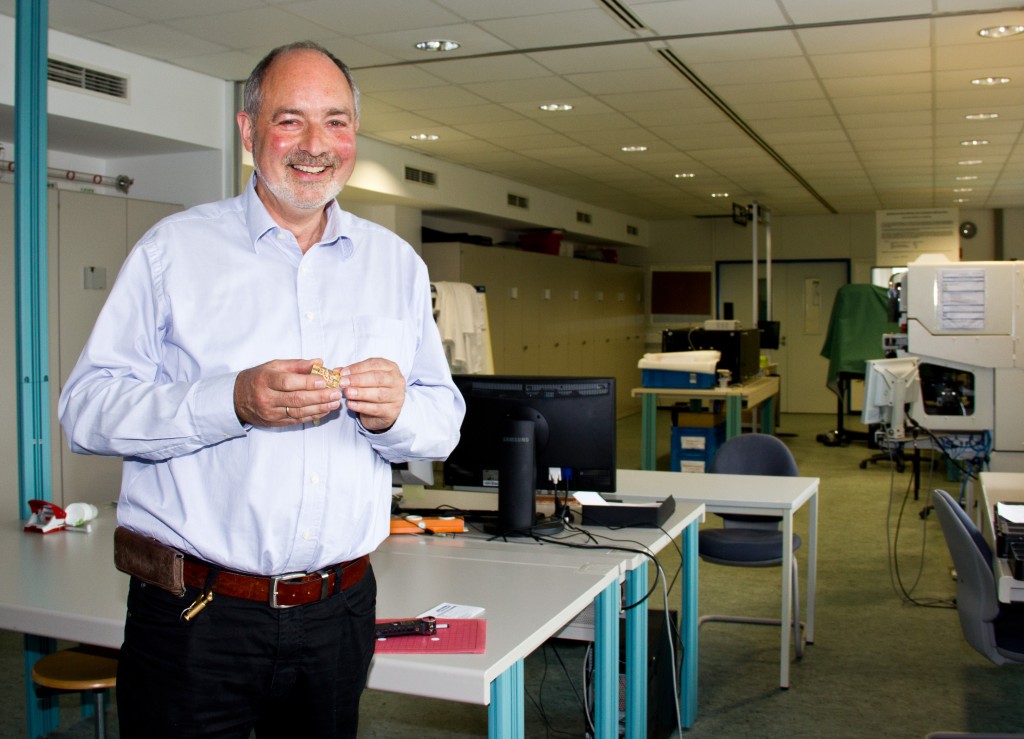
Es braucht mehr als 500 Watt, um die Aufmerksamkeit von Prof. Ronald Eisele zu wecken. 500 Watt, das ist die untere Grenze, ab der man von „Leistungselektronik“ spricht. Innerhalb dieses Teilgebiets der Elektrotechnik sorgen Wissenschaftlerinnen und Wissenschaftler wie Eisele dafür, dass Großverbraucher, etwa Elektroautos, Windkraftanlagen und Schiffsschrauben, sich mit Leichtigkeit steuern lassen und der Strom „sich benimmt“.
Seit acht Jahren lehrt und forscht Prof. Ronald Eisele am Institut für Mechatronik des Fachbereichs Informatik und Elektrotechnik der FH Kiel. Auf einem langen Umweg fand der Physiker zurück an die Hochschule: Über 20 Jahre lang arbeitete er für Industrieunternehmen wie Fibronix und Danfoss Silicon Power, wo er sich vorrangig um die Entwicklung von Messtechnik kümmerte. Am oberen Ende der Karriereleiter angekommen, wurde Eisele als Director Research and Development schließlich jedoch unzufrieden mit dem Verhältnis von Verwaltung und praktischer Arbeit. Rückblickend sagt er, er wollte kein „Papiertiger“ werden – denn das stünde dem entgegen, was ihn antreibt: „Am wohlsten fühle ich mich, wenn ich etwas aufbauen kann.“ Als die FH Kiel 2006 eine Professur für Messtechnik und Integration ausschrieb, packte Eisele die Gelegenheit beim Schopf; seither forscht und lehrt er auf dem Campus zu „echter Technik“. Allerdings will der 56-Jährige die Zeit in der Industrie nicht missen – hat er damals doch viele Kontakte zu Unternehmen geknüpft, die heute als Partner Forschungsprojekte der FH finanziell ermöglichen und das Institut mit Aufträgen betrauen. Aktuell laufen an seinem Fachbereich fünf Förderprojekte und mehrere bilaterale Industriearbeiten. Die größte Herausforderung beim Seitenwechsel aus der Industrie an die Hochschule war für Eisele der Umgang mit den Studierenden. Zwar hatte er bereits zuvor Diplomarbeiten betreut, doch erst an der FH lernte er, was eine gute Rundum-Betreuung ausmacht.

Von der Decke des Labors in Raum 12-3.28, in dem ein eindrucksvoller Maschinenpark steht, hängt ein Schild. „Messen an der Grenze des technisch Möglichen“, steht darauf. „Das ist noch von meinem Vorgänger“, sagt Eisele lachend, „aber an der Grenze zum technisch Möglichen forschen wir auch!“
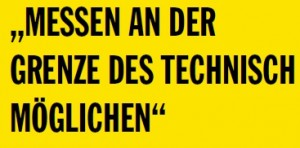
Insgesamt arbeiten eine Ingenieurin, fünf Ingenieure und zehn halbtags angestellte Studierende unter seiner Obhut. „Außenstehende erkennen hier keine typischen Studierenden“, sagt Eisele stolz. Wenn er von seinem Team spricht, lobt er besonders das hohe Maß an Eigenverantwortung und wie arbeitsteilig seine Studierenden vorgehen: „Wir erstellen zunächst gemeinsam einen Arbeitsplan. Dann suchen sie sich Abläufe und Prozesse aus, für die sie anschließend zuständig sind. Die Studierenden sind richtig hungrig auf Verantwortung.“ Um ausfallsicher arbeiten zu können, kennen sich jeweils drei bis vier von ihnen mit jeder der tonnenschweren und komplexen Maschinen aus, die unter anderem mit Druck und Hitze Prototypen herstellen. „Eigentlich unterscheidet uns nur die fehlende Serienfertigung von den Möglichkeiten der Industrie“, erklärt Eisele. „Wir sind in der Lage, alle Produktionsschritte abzubilden. Allerdings steht dazwischen bei uns kein Fließband. Wir tragen die Werkstücke noch selbst hin und her. Fast wie in einer Manufaktur.“

Jeder Mensch kommt täglich mit Leistungselektronik in Berührung, an deren Weiterentwicklung Eisele und sein Team arbeiten. Dass ein Fahrstuhl in der Zieletage nicht rapide stoppt und die Fahrenden durchschüttelt, dass der ICE fast unmerklich anfährt, dass der Kapitän der Queen Mary 2 das 4×22-Megawatt-Kreuzfahrtschiff mit einem Joystick steuern kann – all das ist nur möglich durch Komponenten aus der Leistungselektronik. Eisele hat ein passendes Bild parat, um zu verdeutlichen, was die Leistungselektronik leistet: „Stellen Sie sich vor, Sie möchten aus einem Feuerwehrschlauch tröpfchenweise Wasser entnehmen, um damit eine zarte Blume zu gießen.“ Wann immer es darum geht, große elektrische Ströme zu bändigen, sodass lediglich die benötigte Menge im Spiel ist, kommt Leistungselektronik zum Tragen. Mit Hilfe eines Steuerungsmoduls für einen Fahrstuhl verdeutlicht Eisele die Liga, in der Leistungselektronikerinnen und -elektroniker spielen.
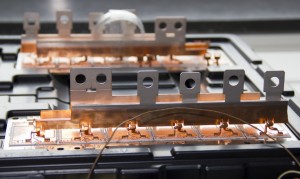
Dicke der Anschlüsse zeigt, wie viel Strom durch
die Bahnen fließt.
Die Anschlussstücke auf der etwa 15 mal 20 Zentimeter großen Platine sind groß und gut zu erkennen, die Kabel und Leitungen entsprechend dick, damit sie unter der durch den starken Strom erzeugten Wärme nicht aufgeben. Wechselhafte Temperaturen sind eine der größten Herausforderungen, mit denen es die Fachleute zu tun haben. Wenn Komponenten unter Volllast fast glühen und anschließend erkalten, macht das dem Material zu schaffen. Dem entgegen stehen die Anforderungen an Schaltmodule: Zuverlässig und langlebig sollen die Bauteile sein, möglichst über Jahrzehnte höchsten Spannungen widerstehen. „Die Betreiber von Windkraftanlagen in der Nordsee haben vor allem aus wirtschaftlichen Gründen kein Interesse daran, immer wieder Technikerinnen und Techniker auf das Meer zu fliegen, damit sie defekte Teile austauschen. Daher investiert die Industrie lieber in hochwertige Komponenten“, erklärt Eisele und stellt stolz heraus: „Die Leistungselektronik ist einer der wenigen Bereiche, in denen Deutschland weltweit führt. Wir hier in Kiel gehören zu den Top-Five-Laboren in Deutschland, die derartige Prototypen für die Industrie entwickeln und bauen können.“ Auch japanische Firmen interessieren sich für das, was in Kiel geleistet wird. Eine Delegation von Mitsubishi war vor kurzem im Fachbereich zu Gast und hat einen weiteren Besuch ins Auge gefasst, ebenso hat sich Hitachi angekündigt, um sich auch außerhalb von Messen auszutauschen.
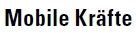
Nicht nur in vielen Windkraftanlagen steckt das Kieler Know-how; auch in zahlreichen Elektroautos finden sich die Leistungsmodule. Wie bei einer elektrischen Bohrmaschine der Abzug steuert in E-Autos das Gaspedal, wie viel Leistung der Elektromotor freigeben soll. Schaltmodule aus der Leistungselektronik sorgen dafür, dass auch nach Jahren ein Tritt auf das Pedal den gewünschten Effekt hat. Eine besondere Herausforderung ist es für die Wissenschaftlerinnen und Wissenschaftler, die Anforderungen von Auftraggebern wie VW oder Audi in Forschungsziele zu übersetzen. Möchte ein Hersteller, dass Schaltelemente zumindest den Lebenszyklus eines Autos von 300.000 Kilometern überdauern, muss Eiseles Team kreativ werden. Schließlich ist keine Zeit dafür, den Prototypen eines Schaltmoduls in ein Elektroauto zu verbauen und damit dann über Monate zwischen Hammerfest und Palermo zu pendeln. Stattdessen errechnen die Wissenschaftlerinnen und Wissenschaftler, wie vielen Belastungszyklen die Module über die angestrebte Lebensdauer ausgesetzt sind und schalten diese in schneller Folge, um zu sehen, ob das Bauteil durchhält.
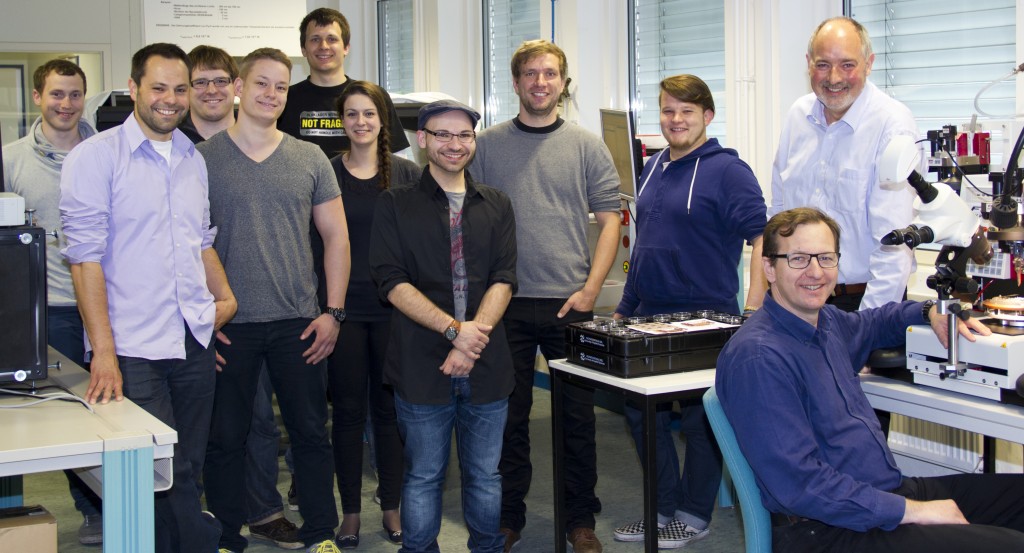
Ganz oben auf dem Wunschzettel von Eisele steht ein eigener Prüfstand, doch dafür sind die FH-Räumlichkeiten nicht ausgelegt. Daher müssen er und sein Team in den letzten Forschungsphasen verstärkt mit der Industrie und anderen Instituten kooperieren und die Auftraggeber die Prototypen im Dauerbetrieb testen lassen. Allerdings hat die Forschungs- und Entwicklungszentrum Fachhochschule Kiel GmbH einen Antrag für den Neubau eines Forschungskomplexes, des Power Research Application Center (PRAC), auf dem Campus gestellt. Wenn alles glatt läuft, wird auf dem Parkplatz gegenüber der Schwentinestraße eine Halle entstehen, die auf die Bedürfnisse des Forschungsteams maßgeschneidert ist. Natürlich habe man auch an die Bedürfnisse der anderen gedacht, räumt Eisele lächelnd ein, denn er weiß um das Konfliktpotenzial des Neubaus: „Die Parkplätze bleiben erhalten, das Gebäude wird auf Stelzen stehen.“ Ein positiver Bescheid wäre das schönste Weihnachtsgeschenk für das Team.


Doch auch auf engstem Raum machen die Kieler Forscherinnen und Forscher große Fortschritte. Lange Zeit wurde in der Leistungselektronik geschweißt und gelötet. Immer kleinere und empfindlichere Bauteile zwangen allerdings zum Umdenken. Die klassischen Verbindungsverfahren, bei denen Komponenten bei einer Temperatur um 300 Grad verbunden wurden, würden die mittlerweile winzigen, filigranen Bausteine zerstören. Eisele und sein Team haben eine Alternative perfektioniert, bei dem Microchips auch bei geringerer Hitze zuverlässig dauerhaft mit Platinen verbunden werden: das Silber-Sintern.
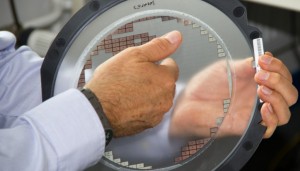
wafer: Die „scharfen“ Bauteile sind bereits vom
Bestückungsautomat abgepickt – zurückgeblie-
ben sind vorgetestete, jedoch defekte Teile auf
dem Klebefilm. Aus diesem Silizium-Rohstoff
werden die Leistungsmodule für die Dosierung
der elektrischen Energie gebaut.
Zunächst tragen sie eine hauchdünne Silberpaste auf die Stelle auf, an der Chip und Platine miteinander verbunden werden sollen. Anschließend fügen sie die Bauteile unter großem Druck und mit einer Temperatur von etwa 250 Grad zusammen. Das Zusammenspiel aus moderater Hitze und Pneumatik sorgt für eine stabile Verbindung, ohne dass die Bauteile leiden. Ein zusätzlicher Vorteil des Sinterns: Im Gegensatz zu anderen Verfahren ist es deutlich umweltfreundlicher. So müssen die Komponenten beispielsweise beim industriellen Löten gewaschen werden, wodurch Abwasser anfällt, das entsorgt werden muss. Als weitere Innovation hat das Team einen Arbeitsschritt entwickelt, bei dem die gesinterte Komponente mit einem hauchdünnen Kupferdeckel versiegelt wird. Dieser schützt die sensiblen Bauteile, wenn diese mit anderen Komponenten per Kupferdraht verbunden werden. Wer allerdings vermutet, dass an den Arbeitsplätzen Töpfe voller Silber herumstünden, den muss Eisele enttäuschen: „Wir benötigen nur sehr geringe Mengen, sonst wäre die Arbeit damit wirtschaftlicher Irrsinn. Zwar ist die Leitfähigkeit von Silber etwa 20 Prozent höher als die des gewöhnlich verwendeten Kupfers, dafür kostet es aber auch das Hundertfache.“

Blickt Eisele in die Zukunft, macht er sich keine Sorgen um die Bedeutung der Leistungselektronik. „Energie ist eines der Themen, die den öffentlichen Diskurs seit Jahrzehnten bestimmen und das nicht an Bedeutung verlieren wird. Es ist ein Mega-Thema, das eng mit anderen wie Finanzen und Umwelt verzahnt ist, und Leistungselektronik ist eine Schlüsseltechnologie“, erklärt er.
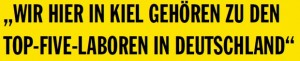
Vor allem die Rückgewinnung von sonst verschwendeter Energie – beispielsweise fließt die Energie, die beim Bremsen eines modernen Autos frei wird, zurück in die Batterie – ist ein interessantes Feld für die Forscherinnen und Forscher. Zudem steigt der Energieverbrauch in Deutschland durch die wachsende Zahl an Single-Haushalten immer weiter und das Interesse an Energieeinsparungen wächst. Doch das größte Energie-Problem kann auch das Kieler Team nicht lösen: „Strom ist viel zu billig“, stellt Eisele nüchtern fest. „Solange elektrische Energie so wenig kostet, gehen viele zu verschwenderisch damit um.“
von Joachim Kläschen